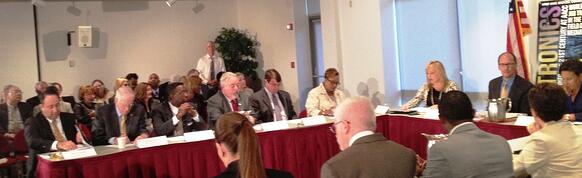
Midway through a recent roundtable discussion on job skills that I attended with others in business, government and education, someone mentioned a need for workers to cultivate co-called soft skills. Thomas Perez, the new U.S. Secretary of Labor, bristled a bit, saying he didn’t like the term: "Let’s change that to essential skills," he said.
He’s right. The ability to write a grammatically correct email to a client, or to calculate diameters and radii to confirm the quality of a manufactured part, isn’t inconsequential. In manufacturing plants like ours and in many other workplaces, these skills are critical. They are essential to the experience you provide to your customer and critical for the success and survival of every business, no matter its size. There is nothing "soft" about them.
During the panel, which was convened to consider solutions to the "skills gap," one panelist said he knew an employer who has kept a position unfilled since 2004 because she couldn’t find the right fit, despite so many people searching for work. The remark elicited gasps.
How do we keep this from happening? Educators must talk more to job creators to learn their needs and to design training that is demand driven. Employers, meanwhile, need to get more active in public-private partnerships focused on job skills. The return on investment for these programs must be made clear to all. We need to borrow from the successful German model of apprenticeships--they seem to serve both employers and young workers very well. We also need an “eHarmony” for internships, as the chancellor of the University of Maryland system put it at the roundtable, to more smartly and systemically pair employers and students.
One area of progress I’ve witnessed in manufacturing is a better alignment between community college programs and industry certifications to make graduates "job ready" and market them as such. A quality welder, for example, should graduate with an American Welding Society certification.
In fact, the Manufacturing Institute, an organization affiliated with the National Association of Manufacturers, has launched a Manufacturing Skills Certification System of nationally portable, industry-recognized credentials. About 175,000 certificates have been issued so far -- about a third of the way toward a goal of 500,000 certificates by 2016. The Institute also launched the “M-List” to recognize high schools, community colleges, technical schools and universities that are teaching manufacturing students to industry standards. Alas, in my home state of Maryland not a single school is on that M-List. That’s not only bad for students, it sends a negative message to manufacturers, and potential manufacturers, in the state.
To bolster student interest, the new U.S. Commerce Secretary Penny Pritzker, who also participated in the roundtable, proposed enlisting broadcasters to try to help improve the profile of manufacturing as a career. As a manufacturer, I think there’s plenty of material to help do that. Making things is cool. Making things in the USA to keep our country strong is cooler yet. The thought can become the thing.
The panelists pointed to successful programs that have set the pace such as "Skills for Chicagoland’s Future" in Illinois. We need more of these at the local level. As Labor Secretary Perez said, the era of “train and pray” is -- or should be -- over.