There are many different ways to finish a custom metal form. From sanding the surface to roughen or smooth it out, to passivating it, to electroplating, to dipping it in a polymer, to electropolishing it, the options are incredibly varied.
One of the most popular finishes for medical and pharmaceutical applications is electropolishing. Electropolishing stainless steel is popular for these applications because it provides several crucial benefits for custom wire and sheet metal forms that are relevant to the industry.
Here’s a quick explanation of the stainless steel electropolishing procedure and its benefits for pharmaceutical and medical applications.
What is the Electropolishing Process?
Electropolishing, or electrochemical polishing, is the electrochemical process of removing material from a metallic workpiece. The process reduces the surface roughness by leveling out microscopic peaks and valleys, which in turn improves the surface finish. This is often used in lieu of mechanically polishing stainless steel, which can be highly abrasive.
How Do Electropolishing Stainless Steel Procedures Work?
Electropolishing stainless steel procedures are similar to passivation procedures in that they use a chemical bath to help strip impurities from the surface of the metal. However, there’s one key difference—electropolishing stainless steel solutions apply an electric current to the solution during the process.
When a current is run through the electrolytic solution, it causes a reaction that dissolves the surface layer of the material being electropolished. This leaves only a microscopically-smooth, almost mirror-like surface.
The Benefits of Electrochemical Polishing and Electropolishing Stainless Steel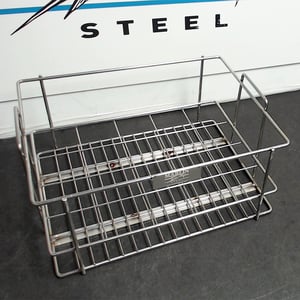
What are the benefits of using stainless steel electropolish versus using a plain surface finish for the medical and pharmaceutical applications? Here’s the shortlist:
1: Improved Sanitation Control for Medical Applications
Sanitation is a key concern for any medical or pharmaceutical application. When medical tools or containers have a rough or uneven surface, that creates small spots where microbes or soils can hide. This increases the risk that some bacteria, viruses, or soils may not be fully sterilized or removed when medical equipment is cleaned.
By electropolishing stainless steel, these microscopic hiding spots are eliminated, giving contaminants nowhere to hide. This makes it easier to fully sterilize electropolished stainless steel equipment between uses.
2: Reduced Galling and Seizing of Medical Mechanisms
Having a microscopically smooth surface helps to reduce friction of parts in complicated medical machinery. This is why manufacturers of medical equipment often apply electropolishing techniques to their products to prevent galling and seizing of equipment.
Frequently, this is used for thin, thread-like materials.
3: Improved Surface Appearance for Medical Equipment
In a medical setting, it can be just as important for a part or tool to look clean as it is for it to actually be clean. After all, a scalpel covered in burn marks at the joint between the blade and the handle wouldn’t inspire much confidence in the sterility of the tool.
Electropolishing procedures strip the surface of stainless steel to leave a clean, smooth, and uniform-looking surface. This makes it easier to tell if the tool or part in question is sterile or not.
4: Reduced Risk of Sharps or Burrs
Another benefit of using stainless steel that has been electropolished is that the process can strip sharps and burrs caused by welds or other metal forming processes. By cutting out sharps and burrs, metal forms can be made safer for manual use.
This helps to prevent minor injuries as well as accidental contamination risks from open cuts in a medical or pharmaceutical setting.
5: Improved Structural Integrity for Stainless Steel Parts
A common issue in parts that have been reshaped is that the shaping process can leave microscopic fissures in the surface of a part. This is especially prevalent in custom metal trays and baskets that have been cold-formed (i.e. bent without being heated up first).
While most medical applications don’t involve the use of forces that would make this an issue, there are somewhere the maximum capacity of a storage or parts cleaning basket might be tested. In these cases, the microscopic surface fractures can be stressed and deepened, weakening the basket.
Since electropolishing removes the surface layer of a stainless steel form, it can also eliminate these microscopic fissures. This helps to make an electropolished wire stronger than a non-electropolished wire of the same thickness by getting rid of the minor flaws that would otherwise be a weak point.
These are just a few of the benefits of electropolishing stainless steel for use in pharmaceutical applications. For more information about how to use custom metal forms for your medical or pharma applications, reach out to the Marlin Steel team today.