With delicate parts, the typical goal is to use minimally-forceful finishing processes so as not to risk damaging the part. However, there are times where to get a part finished right, some amount of force has to be applied.
For one Marlin Steel client, a critical parts washing process involved the use of a washing system that would rotate and upend the parts washing baskets mid-process. This upending motion was used to ensure that agitation was maximized, and that parts would be cleaned more thoroughly and efficiently.
The problem was that this upending motion was damaging their parts in their existing basket design. This contributed to frequent reprocessing or remanufacturing of parts, increasing waste and reducing throughput.
Ensuring Survival for the Parts and the Basket
The immediate problem was that parts could fall out or move around too much and get damaged. To counter this, the basket design needed to create a complete enclosure for the parts.
Another concern was the need for a high-durability basket that could take the shock of harsh agitation without breaking.
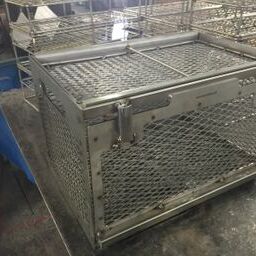
To fulfill both of these needs, Marlin’s degreed engineers started their design with a sheet metal frame that would be the skeleton of the basket enclosure. The heavy-duty sheet metal would provide a strong foundation for the basket that would easily withstand the rough agitation of the wash process.
This design incorporated a locking lid that could be secured shut throughout the roughest agitation cycles, keeping parts securely in place.
However, how would the spaces between the edges of the frame be filled? Wire mesh was too thin to hold the weight of the held parts through the rough agitation cycle of the PROCECO washer. Additionally, securing the wire mesh to the sheet metal would require a lot of welding—increasing labor and time-to-delivery.
On the other hand, sheet metal would obstruct the flow of cleaning fluid through the basket, inhibiting wash performance. Perforating the sheet metal was an option, but there was a faster, more efficient solution: using expanded metal sheets.
Why Expanded Metal?
Expanded metal is created when sheets or rolls of solid metal are passed through an expanding machine that cuts and shapes the sheets. While the holes in expanded metal can be many different shapes, diamond-shaped holes are the most common.
One of the key benefits of using expanded metal is that it allows for the creation of mesh patterns out of a single piece of metal—eliminating potential weak points from woven or welded joints made of two separate materials.
Another benefit is that this process doesn’t produce nearly as much waste material as cutting sheet metal. The metal is stretched and slit to create the holes rather than punched; so there are virtually no wasted bits of metal being punched or cut out.
Using expanded mesh for this basket created an excellent balance between strength, air flow, and material efficiency.
The end result was a basket that could safely hold the client’s parts through tough cleaning cycles day in and day out without breaking.