Welding is a key process in the creation of almost any custom steel wire or sheet metal form—from the smallest trays to the biggest stainless steel carts. When most people think of welding, they usually picture a person in overalls holding a gas torch to large piece of metal and trying to melt the metal together.
However, modern welding techniques are much more varied than what the average layman would assume. There are many different kinds of welding equipment and welding techniques that manufacturers working with metal use beyond the traditional gas torch process that most people think of.
Some of the types of welding processes frequently used by Marlin Steel include:
Tungsten Inert Gas (TIG) Welding
TIG welding, also known as gas tungsten arc welding (GTAW), is an arc welding process that uses a non-consumable electrode made of tungsten to run an electrical current through metal. The metal’s resistance to this current causes it to heat up, allowing it to bond with other materials by melting into them.
Depending on the specific machine and process used, a TIG weld may or may not use a filler material to join two pieces of metal.
Metal Inert Gas (MIG) Welding
MIG welding, also known as gas metal arc welding (GMAW) is similar to TIG welding, but there’s one distinctive difference: MIG welding employs a consumable metal wire as its electrode. The metal wire melts during welding, becoming a filler material to help join the objects being welded.
Because of this, MIG welds don’t have to heat the actual objects being joined to their melting point—the filler material can instead serve as the bonding agent.
Resistance Welding
Like arc welding, resistance welding employs an electrical current to help join two pieces of metal together. However, unlike arc welding techniques, resistance welding doesn’t use filler material. Additionally, pressure between the two materials being joined is a much larger factor for determining weld quality in a resistance-welded joint than it is for an arc-welded one.
Having too much or too little pressure on the weld joint can compromise weld performance and lead to a number of different issues.
Upset Butt Welding
Butt welding is a specific type of resistance welding where the two surfaces to be joint are pressed together prior to the welding process. When performed correctly, this process largely eliminates the splatter from the welding process, creating a smooth weld with little expulsed material.
Types of Welds
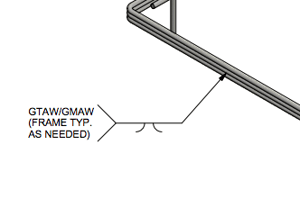
Aside from specifying the welding technique, Marlin Steel also sets the specific type of welding action to be used in its custom metal form basket design documents. In the design document, these instructions are relayed via different weld symbols.
Some typical weld types include:
- Fillet Welds. Represented by a right-angle triangle symbol, fillet welds are typically used to join two pieces of metal at a perpendicular angle. For this reason, they are sometimes called T-welds (or tee welds).
- Spot Welds. Like the name implies, spot welding is the joining of two pieces of metal by welding a specific spot on one piece of metal to another. It’s comparatively economical because the size of the weld is so small compared to other weld types. These welds are represented by a circle.
- Square Groove Welds. This is another name for butt welding, where two workpieces are pressed flat together prior to welding. This type of weld is represented using a flat line.
- Flare Bevel Groove Welds. Represented by a curved line, flare bevel groove welds are generally used to join a rounded or curved piece of metal to a flat one.
- Slot Welds. A type of weld where two pieces of overlapping metal are pressed together. One piece of metal has a slot cut into it (hence the name “slot weld”), through which the other piece of metal is accessed for welding. This is represented with a rectangular weld symbol.
These symbols let the person programming the welding equipment to know exactly where and how each weld should be placed to most closely match the intended performance characteristics of the design.
Marlin’s engineering team has years of experience in choosing the best welding tools and techniques to help our customers get the most out of their custom metal forms. If you need help engineering the perfect custom wire or sheet metal basket for your needs, contact us today for a custom basket quote!