Over the years, the manufacturing industry has changed. One of the major forces driving recent changes is the ever-evolving technology that gets used by American manufacturers.
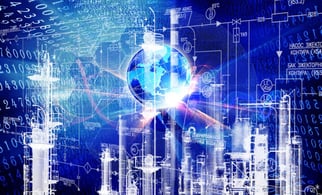
Every year, there are countless new innovations made that can be applied to manufacturing processes. From new equipment, to new software, to new processes, to new methods of organizing manufacturing tasks, U.S. manufacturers are constantly updating their toolkits to remain competitive.
However, a side effect of all of this investment in technology and the “Internet of Things” (devices connected to networks to streamline management and operations) is that there is now an even more powerful demand for skilled workers in the manufacturing space.
How the Use of Tech Drives the Demand for Skilled Workers in the American Manufacturing Industry
For example, in a Manufacturing.net article titled “Managing Change in the Manufacturing Revolution,” Mike DiLeo, the Operations Director with the Management and Strategy Institute, cites that there is a “skills gap reflected in the lack of knowledge about IT integration, how to assess time-saving efficiencies and other process values, how to make data-driven decisions.”
The author ties the technology skills gap to a paralysis amongst some enterprises that keeps them from integrating “potentially game-changing procedures and technologies.” After all, if there’s nobody on the staff who can effectively use the new equipment or knows the procedure, then how can a company adopt that big new innovation?
In this way, the use of technology in the American manufacturing industry is helping to drive the demand for skilled workers in manufacturing.
Addressing the Issue with the Skills Shortage
While there is a lot of demand for workers who have the big Six Sigma-related skills to enact lean manufacturing, there just aren’t enough skilled applicants out there to fill the jobs that American manufacturers need to fill.
While most manufacturing jobs don’t require a college degree, many of the high-tech machines used by manufacturers do require some form of computer programming knowledge to operate, as well as some basic mechanical engineering knowledge to maintain in top working condition.
Some machines require very specific training to operate, and not many applicants may even know that a specific machine exists, let alone possess detailed knowledge of how to operate and maintain said machine for peak efficiency.
I covered how U.S.-based manufacturers can address the skills gap in another post, but here’s a solution that bears repeating: invest in training your existing employees to give them new skills to match your needs.
Marlin Steel, for example, has a skills matrix posted in the break room that lists all of the skills needed by the company, and who has what skills. Just having this board on display encourages the competitive spirit among Marlin’s workers. Employees compete with each other to see who can master the most skills and fill the most spots on the board.
The learning of new skills is further incentivized with a permanent pay increase for learning certain skills. The more the skill is needed, and the more effort it takes to learn, the bigger the bonus.
Marlin sets aside 5% of it’s payroll for training budget so that employees have the opportunity to pick up the skills Marlin needs to be the most efficient and effective manufacturer that it can be.
This training focus has the benefit of creating redundancy for many skills so that operations don’t get crippled when one employee takes a leave of absence.
Innovations Drive Tech Adoption, Tech Adoption Drives Need for Skills, Filling Skills Needs Drives Efficiency
The search for increased efficiency is a never-ending journey for manufacturers. In the search for greater efficiency, many manufacturers will adopt a new process or technology that can save them time, labor, or material.
When that new innovation requires a specific set of skills or knowledge, that manufacturer then has a need to acquire workers with those skills. This can mean hiring a new worker with the aforementioned skills/knowledge, or it can mean having to train an existing employee so they have the necessary talents and abilities to make the most out of the new process or equipment.
These new skills can help provide a manufacturer with employees who have skills and knowledge that can be leveraged to further improve productivity and efficiency.
For example, as Mike DiLeo mentions in his article about the benefits of Six Sigma training, “some businesses – those who are firm in their DMAIC methodology and require their high-level Black Belts to produce results in order to be fully certified – see even more robust returns, and the investment on those Black Belts is a 7:1 cost-to-savings ratio.” This demonstrates how a focus on efficiency training can help a company be much more more effective.
At Marlin Steel, the skills training of employees allows them to more intimately understand production processes, empowering them to find ways to optimize production efficiency to save time, labor, and materials. In this way, it can be said that driving skills growth among employees helps to drive efficiency for the manufacturer.
As time goes on, and new innovations are introduced to the manufacturing industry, the need for skilled and adaptable workers who can leverage these innovations will continue to grow.
With this in mind, finding ways to address the growing skills shortage faced by the American manufacturing industry is of paramount importance.
What are your thoughts on the skills shortage and the adoption of new technology and processes by U.S. manufacturers?