From Drew Greenblatt's latest column on Inc.com about the importance of workplace safety:
On a recent visit to a Fortune 100 company, one of the world’s largest manufacturers, I asked the company president how he assesses the performance of his company as well as prospective vendors. He mentioned market share, cash flow and profit -- key indicators all -- but I was astounded at what he mentioned first: Safety.
"Have you ever heard of an unsafe shop being clean or making good quality products?" he asked.
It’s true. An obsession about safety in a workplace is a pretty reliable signal that the company is compulsive about other processes, such as making a quality product. If cleanliness is next to godliness, it’s also pretty close to industriousness and dependability.
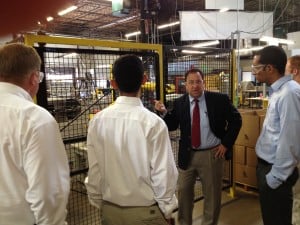
Before I bought Marlin Steel, I noticed that a couple of the factory workers were missing fingers. A couple others had lost eyes. The staff at the time didn’t seem frightened or unnerved by this, but it shocked me. On my first day on the job, I bought a bunch of safety glasses and insisted that everyone wear them. That didn’t go over well. I was met with resistance. Even in a place where industrial risk was painfully evident, workers considered the glasses intrusive and a pain. But buy-in came eventually along with a realization that a safer company is a healthier company, in more ways than one.
My company has now gone more than four years without a lost-time accident, more than 1,700 consecutive days. The benefits to workers are obvious and significant: better health, less injury, less pain, less disruption. There were additional benefits to the organization that I probably could have predicted when we embarked on a safer culture such as cheaper insurance premiums, workers missing less time, other workers not having to fill in for injured co-workers.
But there were additional rewards I hadn’t foreseen: Employees seem to appreciate working for a company that has their well-being at heart. And a focus on safety resonates with clients and prospective customers as well.
When you’re buying something from a company, especially if you’re contemplating a long-term relationship with a supplier, you want to know you can trust the folks you’re dealing with, that they’re a stand-up group. A great safety record is a sign that the organization, particularly in a manufacturing arena like ours, is focused, vigilant and professional in its approach. The finer points of producing custom-engineered steel and wire containers for material handling -- what we do -- aren’t always so easy to translate to those who are outside our day-to-day business; a magazine writer, for instance, recently described our business as an “esoteric … quirky corner of the economy” -- and he meant that as a compliment! But everyone - whether it’s a prospective customer, new employee or community member -- grasps the value of a going many days without an accident.
Our initial push for greater safety was, well, to just keep our folks healthier and safer. But a funny thing happened on the way to 1,700-plus consecutive days without an accident: It’s become a defining value for us as well.