American manufacturing companies adopted the use of automation systems like robotic welding to help them stay competitive in the market, keep up with demand, and work more efficiently.
The best part about automation and robotic welding is that it doesn't mean the end of American manufacturing jobs. Trends in automation change and evolve significantly over time, making it easier for manufacturing workers to complete tasks.
These trends are impacting robotic welding in many ways.
What Is Robotic Welding?Robotic welding is an automated welding process where two materials are fused together through heating, mixing, and cooling using mechanized programmable tools.
Robotic welding is best for industrial and manufacturing industries with high-volume, repetitive welding processes. There are several types of welding processes that can be completed using robotic welding tools.
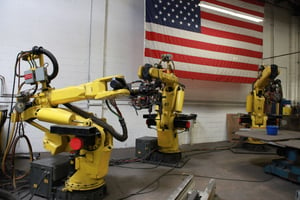
Some of the most common forms of robotic welding include:
- Resistance welding
- Spot welding
- Arc welding
- TIG welding
- Laser welding
- MIG welding
- Plasma welding
Robotic welding offers various benefits, such as increased efficiency, increased safety for production workers, and a reduced need for manual adjustments in the welding process.
Your manufacturing efforts can benefit greatly from the use of robotic welding machines that help you to keep up with automation trends.
5 Automation Trends Impacting Robotic Welding
Here are five current automation trends that impact robotic welding.
1. Production Monitoring
As manufacturers try to increase production speed, they turn to production monitoring systems. These systems yield more accurate measurements, manage processes more efficiently, and increase part quality.
They also monitor and provide input on the quality of the weld. This allows manufacturers to manage the quality output of robotic welding machines.
Production monitoring systems offer huge time savings for production line managers, which allows your manufacturing process to be faster without sacrificing quality.
2. Adaptive Welding Advancements
Sensors have been added for adaptive welding to make robots user-friendly for more flexibility and speed.
Sensors give robots a sense of touch and sight as they move along a weld seam. This makes it easier for for them to communicate more detailed information, instead of just data.
3. Upstream Practices
Upstream practices must work properly with the weld cell to make sure the right type and quantity of parts are available for the welding application.
Marrying upstream processes and weld cells reduces material handling time, saves floor space and resources, and ensures the entire operation flows smoothly.
4. Collaborative Technology
Having a human operator and a robot in close proximity to one another ensures safe and efficient operations. Some of the new collaboration trends between robot and operator include gesture commands to generate a specific action or program.
5. Easier Programming and Operation of Robotic Automation Systems
Proper robotics training is needed in the manufacturing environment, especially for programmers. This way, they can program the automation systems correctly according to what is being manufactured.
Robotics automation systems have changed to become more user friendly.
Many systems now offer elements like offline programming, wireless communication systems, and sensor technologies. Programmers will need to cultivate a deep understanding of the many manufacturing environments that use robotic welding in their processes.
Marlin Steel's employees and highly skilled engineers use automation and robotic welding systems to make products that are more durable and of the highest quality for your needs.
Contact Marlin Steel to learn more about their superior products and see what custom solutions are the best fit for you.