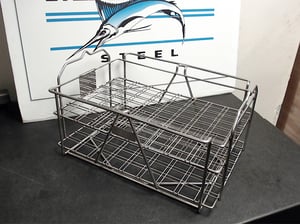
What Is NDT (Non-Destructive Testing) for the Aerospace Industry?
Aerospace parts constructed with flaws and incongruencies can lead to catastrophic failures. This risks the health and lives of operators along with a great deal of funds. Materials, parts, and components must be tested for safety and reliability using a diverse list of inspections through every stage of production.
In the aerospace industry, non-destructive testing (NDT) is a critical component in efforts to decrease the risk of potentially fatal failures.
What is NDT?
Non-destructive testing is a testing and analysis technique used to examine the properties of a material, component, or structure for defects without changing or damaging the part. Flaws and irregularities can be easily identified without disrupting the integrity of the subject.
NDT methods are crucial to the aerospace industry, serving as the final line of defense against undetected issues that could jeopardize the safety of spacecraft, aircraft, and other aerospace components. By detecting defects before they can compromise structural integrity or cause catastrophic failures, NDT procedures offer a preventative and proactive approach to ensuring safety and reliability for manufacturers. Additionally, NDT acts as quality assurance during aircraft testing and certification. This prevents a potential loss of revenue, unsafe conditions, and the need for expensive repairs or parts replacements resulting from failed products or equipment.
Marlin Steel produces custom stainless steel products for the aerospace industry, from cleaning baskets to custom carts. Most NDT methods, particularly ones that require the use of fluids like liquid penetrant testing, require the use of aerospace NDT dipping and drying baskets to aid the process.
What Are NDT Methods?
There are several non-destructive testing methods that can be applied at every stage of a product’s construction.
Liquid Penetrant Testing
Liquid penetrant technology is the most cost-effective for routine “in-house” inspections during engine maintenance, repair, and overhaul (MRO) operations. The process is highly productive and encompasses several steps to guarantee reliability.
The product is cleaned and dried before a liquid penetrant is applied. The fluid will seep into any defects (i.e. cracks, holes, etc.) and dry inside it. After the excess penetrant is rinsed away and developed, there will be a visible indication of any defects present.
Acoustic Emission Testing
This NDT method uses sensors to detect short bursts of ultrasound emitted by cracks or gaps in a surface. Leaks, active corrosion, and highly stressed areas can be detected with acoustic emission testing, making it an ideal practice during proof tests of pressure vessels.
Electromagnetic Testing
There are three types of electromagnetic testing: eddy current testing, alternating current field measurement (ACFM), and remote field testing (RFT). In all three methods, a magnetic field or electric current is passed through a conductive component.
- Eddy Current Testing: Uses an alternating current coil to create an electromagnetic field into the component.
- ACFM: Uses a probe to introduce a magnetic field.
- RFT: Uses a similar method to ACFM, but is traditionally used when testing pipes.
Ground Penetrating Radar
Radar pulses are sent through the surface of rock, ice, water, or soil, and the waves are reflected back or refracted when they hit another material or object with different properties.
Leak Testing
This method is divided into four different NDT processes: bubble leak testing, pressure change testing, halogen diode testing, and mass spectrometer testing.
- Bubble Leak Testing: A tank of either a liquid or soap solution is used to detect gas leaking from the product via bubbles.
- Pressure Change Testing: Monitors the loss of pressure or vacuum in a product to indicate a leak.
- Halogen Diode Testing: A halogen-based tracer gas is mixed with a halogen diode detection unit to identify any pressure changes, indicating a leak and locating it.
- Mass Spectrometer Testing: Helium is used with a halogen diode detection unit to detect changes in the air sample of a product, indicating a leak.
Laser Testing Methods
Laser testing is divided into three different processes: holographic testing, laser profilometry, and laser shearography.
- Holographic Testing: A laser is used to detect changes in the surface of a material that has been stressed by heat, pressure, or vibration. Results are then compared to an unstressed reference sample to show any defects.
- Laser Profilometry: A high-speed rotating laser is used with miniature optics to identify corrosion, erosion, cracks, and other flaws by detecting changes in a surface with a 3D image generated from the process.
- Laser Shearography: A laser light creates an image before a surface is stressed and after. The images are then compared together to identify any defects.
Magnetic Flux Leakage
A powerful magnet is used to create magnetic fields to saturate steel structures. Sensors are then used to detect any changes in magnetic flux density, which indicate erosion, corrosion, or pitting.
Magnetic Particle Testing
Magnetic particle testing requires the use of magnetic fields to identify flaws on the surface of ferromagnetic materials. The magnetic field identifies disparities via magnetic particles that are drawn into the location of any leaks.
Microwave Testing
Used only on dielectric materials, microwave frequencies are transmitted and received by a test probe that will detect any changes in properties, indicating flaws.
Radiographic Testing
This NDT method uses radiation passed through a material or part to detect any flaws. X-rays or gamma rays are used to produce a radiography to distinguish any discontinuities in the product.
Neutron Radiographic Testing
A beam of low-energy neutrons is used to penetrate an organic material or surface during this test. Organic materials allow the beam to be seen, wherein internal components can be examined and inspected for flaws.
Thermal/Infrared Testing
The wavelength of infrared light emitted from an object is measured by sensors in this method’s two process types: passive thermography and active thermography.
- Passive Thermography: Overheating temperatures for motors and other electrical products can be estimated via digital readings of the emitted radiation.
- Active Thermography: A temperature gradient is induced through a product and allows for any structures inside affected by the heat to be analyzed and any defects identified.
Ultrasonic Testing
Ultrasonic testing uses high-frequency sound by transmitting it into a product and recording any materials within the product that reflect or weaken it. Disparities are then able to be identified and located.
Vibration Analysis
A vibration analysis uses sensors to measure the vibration signatures from rotating machinery. The condition of the equipment is then assessed for any discontinuities.
Visual Inspection
A material, part, or component is examined by an operator for any signs of damage or flaws with the use of optical instruments. This NDT method is often used during the performance of other tests as well.
The Benefits of NDT
There are several ways that NDT inspections benefit aerospace manufacturing.
Accident Prevention
Safety is the top priority in aviation. Therefore, the production and construction of aerospace materials and components require thorough analyses and inspections throughout a product’s lifecycle. Any flaws in the surface or subsurface of a product could result in catastrophic failures.
When NDT methods are practiced at each stage of development, defects and discontinuities in materials can be identified before they become problems that create a need for repair or replacement. As a result, aircraft parts are crafted and assembled with their integrity intact—decreasing risk and the chance of accidents occurring.
Improved Product Reliability
When defects are identified in earlier stages of development, it reinforces the reliability of a product. Non-destructive testing points out these discrepancies without the need to damage or deconstruct a product or material, unlike destructive testing that requires the destruction of a product to yield results.
With NDT methods, manufacturers and researchers can have confidence in the products that they’re producing and sending out into the world.
Improved Repair Insights
While performing non-destructive testing and inspections, potential repair or replacement needs can be identified as flaws and inconsistencies present themselves. Issues can then be addressed promptly as they appear—though there aren’t any guarantees that they won’t appear again in the future.
Researchers can take note of which flaws may appear again in the future and anticipate when repairs will be necessary. The longevity of a component or material can also be estimated based on the results of NDT.
Cost Reduction
Flaws or irregularities that fly under the radar during production can lead to expensive repairs and replacements that will cut into an organization’s budget. The cost is compounded even more if the product is damaged beyond repair and has to be disposed of.
The NDT process is designed to identify issues long before they become a much larger financial investment than necessary.
Meeting Industry Standards
NDT methods are critical for not only ensuring that aerospace products meet safety requirements but also for maintaining compliance with strict industry standards and certifications.
- EASA and FAA: Regulatory bodies such as the European Aviation Safety Agency (EASA) and the Federal Aviation Administration (FAA) have set forth strict requirements surrounding the design, manufacture, and maintenance of aircraft. NDT plays a key role in ensuring compliance with these standards.
- Airworthiness Certification: All commercial aircraft must obtain an airworthiness certification prior to operation. NDT procedures are integral to the certification process, providing a way to certify that the aircraft and its components meet the necessary performance and safety requirements.
In addition to the above standards, NDT is a fundamental tool in driving continuous innovation and improvement in inspection technologies. This helps to stay ahead of emerging challenges and risks in the ever-evolving aerospace industry.
Aerospace Applications of NDT
Non-destructive testing is implemented across several stages of the aerospace manufacturing process. From examining raw materials to inspecting the final product and performing maintenance, NDT is paramount to ensuring the safety and integrity of aerospace systems.
Aircraft Maintenance
NDT is used as part of routine checks and preventive maintenance procedures to verify that all components are still airworthy. These processes include thorough inspections of the following:
- Aircraft engine components (such as turbine blades)
- Aircraft skin
- Bolt holes
- Fuel tanks
- Landing gear components
- Welds
- Wings, fuselages, and other composite materials
Manufacturing Processes
Aircraft makers use NDT methods to ensure the quality of joining processes and raw materials both during and after manufacturing. By performing in-depth testing at regular intervals throughout production, manufacturers can detect issues early on and make necessary corrections to guarantee the safety of all components.
How Marlin Steel’s Products Support Aerospace Non-Destructive Testing
Marlin Steel produces top-quality custom stainless steel wire products or the aerospace industry, from cleaning baskets and blade & vane baskets to custom carts. Most NDT methods, particularly ones that require the use of fluids like liquid penetrant testing, require the use of aerospace NDT dipping and drying baskets to aid the process.
With neoprene liners that prevent metal-on-metal contact, your test pieces will maintain their integrity without the risk of damage or incontinuities occurring.
Need custom wire baskets for your aerospace non-destructive testing inspections? Contact the experts at Marlin Steel to get a quote, or for more information about Marlin’s custom wire form manufacturing process.