Manufacturing scrap is often considered an inevitability, something that just happens as a natural consequence of the manufacturing process. While some manufacturing waste from scrap production is inevitable, scrap production can actively detract from your company’s bottom line.
How so? The scrapping of whole parts part of the way through production wastes the materials and labor spent on the manufacturing process. In a best-case scenario, the scrapped part can be refinished and put to use (meaning only some time and labor is lost). However, in a worst-case scenario, the part may have to be thrown out entirely to be recycled into raw materials (assuming the part can be recycled). This can be incredibly wasteful of both resources and valuable manufacturing time.
So, eliminating scrap in the manufacturing process is an important part of lean and competitive manufacturing processes. How can you reduce manufacturing waste and scrap in your parts making processes? Here are a few ideas that you may be able to employ in your own production line:
Scrap Reduction Tip #1: Minimize Manual Handling of Delicate Parts
Marlin Steel’s manufacturing team use factory automation for a great number of reasons, including safety. Not just for the workers themselves, but for the parts that are being assembled—which helps to minimize manufacturing scrap from damaged parts.
How does automation help eliminate scrap in manufacturing processes?
First, machines don’t get sick or tired the way manual laborers do. A machine doesn’t get a muscle spasm because of a repetitive motion stress injury or sneeze and drop a multi-thousand-dollar load of small, delicate, no-scratch parts all over the floor.
If you can set up a machine to handle a given task in a way that doesn’t risk damage to the parts you manufacture, then automating that process is often the best option. Not only will you save money on reprocessing your parts, you’ll improve your time to market by getting parts right the first time.
This is often easiest when your production process uses specialized steel wire baskets to hold parts from one phase of your process to another, which helps to limit physical contact with your delicate manufactured parts.
Scrap Reduction Tip #2: Use the Right Metal Forming Tool for the Job
Reducing scrap in manufacturing processes means more than just making cuts efficiently—it requires using the right tool for the job to maximize efficiency. The tools and techniques you use to shape metal forms go a long way towards reducing the amount of excess scrap that is created during your manufacturing process.
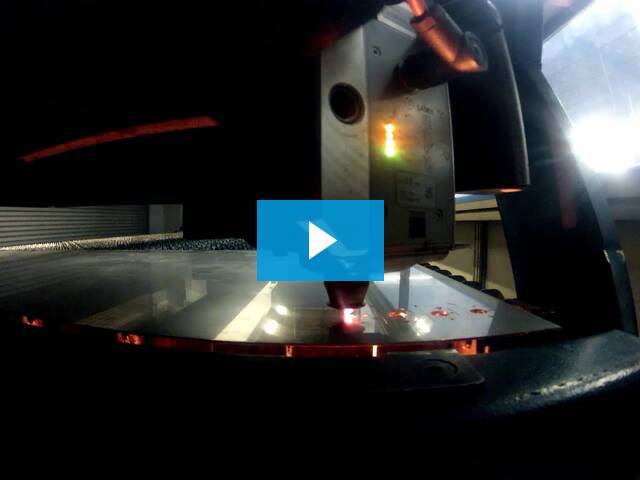
For example, here at Marlin Steel, we use a number of different machines to cut and shape steel sheet metal, including:
- A CNC Metal Punch. With the Trumpf CNC punch, Marlin Steel can both cut and make bends in sheet metal forms. For large work pieces, the ability to make bends at the cut site can help to conserve materials and production steps for more complicated sheet metal forms—which helps minimize manufacturing scrap.
- A Cutting Laser. Laser cutters such as the Trumpf TruLaser 1030 allow for incredibly precise cuts to be made in sheet metal with very smooth edges. When cutting shapes out of a sheet metal plate, laser cutters can make cuts incredibly close to one another, maximizing the number of forms that can be made from a single plate of sheet metal and minimizing manufacturing waste.
The choice of machine to use depends on a number of factors, such as whether or not the sheet metal needs to be bent into specific shapes. By choosing the right tool for the job, scrap can be kept to a minimum.
Other tools that you might want to take a closer look at include the containers that you use to hold your parts through the production process. Inefficient container designs contribute to part damage and scrap production during late-stage production processes such as ultrasonic parts cleaning or heat treating.
Sometimes, eliminating scrap may be as simple as revising the design of your parts cleaning baskets for better handling of parts.
Scrap Reduction Tip #3: Keep Employees Trained and Motivated
No matter how heavily you’ve invested in factory automation, your people are still key to your company’s success. It’s your workers who set up, operate, and maintain the machinery that you use to meet your production goals. Keeping their skills up to date while motivating them to find ways to improve efficiency is a key part of eliminating scrap.
How so? Here’s a hypothetical scenario:
Say that you have a part that you need to produce, and want to optimize the process to eliminate scrap and save money. You hand the task of creating the part to two teams of workers, team A and team B.
Team A consists of workers who have trained with all of your manufacturing equipment and have detailed knowledge of manufacturing processes and the mechanical properties of the materials you work with. Team B has no such experience or training.
Which team would you expect to be more successful at eliminating waste in the production process and staying on task?
The team with the greater knowledge and training will naturally be better at reducing scrap and other forms of waste that cost your company money. They’ll make smarter use of your resources, and not have to go through nearly as many “trial and error” experiences to find out what does and does not work.
Finding ways to keep these employees motivated to reduce scrap is another challenge altogether.
One method that Marlin Steel has had success with is the use of a performance-based bonus program that rewards employees for meeting aggressive production goals. These goals are difficult, if not impossible, to meet with wasteful processes, so employees are motivated to seek efficient solutions to production challenges that reduce scrap.
Reducing Scrap Tip #4: Consider the Containers for Your Products
It happens all the time—freshly-made parts go into one end of an ultrasonic parts cleaning or parts finishing process, and scratched-up junk comes out the other end that has to be scrapped. This is often because the containers used to hold the parts aren’t built in a way that properly protects the parts they hold. Instead, they were built on the cheap to fulfill a basic operating requirement.
The problem with these minimalist container designs is that they fail to take into account the specifics of the manufacturing process and the design of the parts they hold. This leads to an increase in damaged parts that have to be scrapped. So, these “money saving” baskets end up costing more in the way of manufacturing scrap and wasted time than they save in up-front expenses.
Using a custom wire basket or sheet metal form that is optimized for the specific manufacturing application is crucial for eliminating scrap from parts damage. For example, adding a soft polymer coating to an ultrasonic cleaning basket can prevent metal-to-metal contact during the cavitation process—eliminating the risk of scratches and dents that cause parts to be scrapped or need remanufacturing.
Learn More about Eliminating Scrap and Manufacturing Waste
Consult with a mechanical engineer from Marlin Steel today to learn how you can further improve your production process to make it ultra-efficient and reduce scrap production. To see how Marlin Steel has helped other manufacturers reduce scrap and improve efficiency, check out the case study at the link below: