Robotic technologies are being used more and more in manufacturing plants small and large, and even in project-based workshops.
Robotic welding is a costly investment, but it also starts to improve the bottom line of your business performance from the first day you begin operating it.
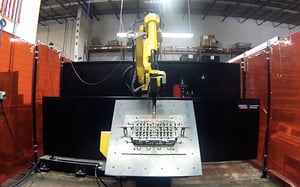
Two of the most common welding technologies used in factories across the U.S. are metal inert gas (MIG) and tungsten inert gas (TIG) welding.
4 Benefits of Robotic Welding
Here are four key benefits for you to take advantage of when you use robotic welding.
Enhanced Safety
Quality robotic welding systems streamline repetitive key process and help humans avoid dangerous tasks. This means a much lower error rate, and it provides team members with the option to focus on more important challenges.
Robots also are able to work longer hours than humans without management worrying about fatigue or burnout, which can lead to more mistakes and workplace safety issues.
Increased Efficiency
This aspect is one of the reasons many businesses decide to consider robotic welding. The consistency of workflows and the quality of materials also plays a role in the efficiency and quality of robotic welds.
But when those issues become systemized, a robotic welding machine provides exceptionally high-quality and efficient welds.
Less Waste
Over-welding is one of the biggest waste sources for any welder. It often costs businesses thousands of dollars, even on small projects. Robots use high precision specifications to ensure there is less cost for metal filler.
Better Accuracy
Robots weld with accuracy no matter how complex the task is. Almost everything in a robotic welding system can be routinized to a degree that provides the most accurate output possible. Users who operate the robotic systems are easily able to adapt to new projects no matter how innovative they may be.
What Is Robotic TIG Welding?
Robotic TIG welding, also known as Fas Tungsten Arc Welding (GTAW) refers to a high-quality welding process that uses a tungsten electrode, or non-consumable welding wire.
A current runs through the metals to heat and join them together. A robotic TIG welder uses a computerized controller for timing welding operations and a robotic arm assembly for moving the welding tip into place.
What Is Robotic MIG Welding?
Robotic MIG welding refers to a type of Gas Metal Arc Welding (GMAW) that uses a continuously feeding metal wire electrode into the weld being made. The consumable welding supply of the wire acts as a filler material to help join the two metal objects.
Since the electrode becomes a filler material, this welding process doesn’t have to melt the metals being joined to achieve a weld.
The Key Differences Between TIG Welding and MIG Welding
A little confusion is perfectly normal. After all, both MIG and TIG welding procedures use electrical arcs to produce heat and join metallic objects. Also, both processes use an inert gas mixture to prevent the corrosion of welding electrodes.
But, there are some key differences between these two electrical arc welding processes which affect when you would want to use one or the other:
Here are a few things that differentiate TIG and MIG welding.
- Unlike MIG welding, the TIG welding procedure may or may not use a filler metal for the welding supply.
- A filler is not always needed in TIG welding but is used when welding together metals with high melting points to prevent cracking.
- MIG welding employs a consumable filler material to make welds; it can often complete welds of thicker metal objects in less time than a TIG weld.
- TIG welding works best for joining smaller pieces of metal, such as the wires for a custom steel wire basket.
- Using TIG welding for direct metal-to-metal welding produces a neater and more attractive finish without needing extra steps such as electropolishing.
- MIG welding tends to be a bit more forgiving of mistakes than TIG welding is – so it’s often recommended for first-time operators and non-professionals.
How to Choose the Right Robotic Welding for Your Application
The right robotic welding type for you depends on the job you are trying to complete. As we discussed earlier, MIG welding is usually better for heavy-duty welding work where larger, thicker pieces of metal are being joined because it uses filler material.
If metals are especially thick, then MIG welding may be more effective for your project.
However, TIG welding works well for joining small pieces of metal together flawlessly. For example, Marlin uses TIG welding to join the wires for a custom steel wire basket.
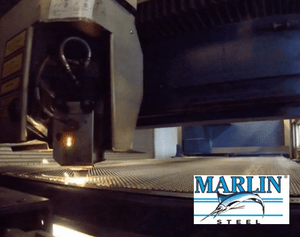
Consider how TIG welding can be a bit lower maintenance, since the welding electrode isn’t being constantly consumed by the welding process. However, TIG welding will likely always cost more than MIG since TIG is a much more tedious process.
While the actual materials used in TIG welding are only slightly more expensive than in MIG welding, it's the length of time it takes to weld using the TIG method which makes this welding process more costly.
In short, the best welding solution for you should be selected on a case-by-case basis, which is why Marlin Steel is dedicated to having a range of tools and technologies for completing welds according to your requested materials and preferences.
If you don't know which metal arc welding process would be the best for a given task, Marlin is here to help. They use their state-of-the-art Lincoln robot welder for both MIG and TIG welding. This machine has powerful laser touch sensing and a tilting and rotating positioning table for faster, safer, and consistent welding every time.
Marlin’s engineering team also double checks the needs of your application assumptions using virtual physics simulation software to verify that the welded joint will perform as expected.
Contact the experts at Marlin Steel to get your custom wire basket to fit your needs seamlessly.